Harnessing the Power of Microturbines: Steam Generation with Capstone Technology
Microturbines have been heralded as a versatile and efficient solution for power generation for almost 35 years. Among the vanguard in this field is Capstone Green Energy, a pioneer in the development of advanced microturbines. As energy demands continue to rise, the need for innovative and sustainable solutions is more crucial than ever. In this article, we will explore how Capstone microturbines not only offer reliable power generation but also open doors to highly efficient steam generation.
Capstone Microturbines: A Leap in Power Generation
Capstone has been a game changer in the realm of distributed energy generation. The company's microturbines are lauded for their low emissions, compact size, and reliability. A cornerstone of Capstone's success lies in the versatility of applications - from standalone power generation to cogeneration and trigeneration systems. Moreover, Capstone microturbines require minimal maintenance, as they employ air bearings and have only one moving part. This translates to lower operational costs and a smaller carbon footprint, making them an attractive option for businesses and industries.
The Intersection of Microturbines and Steam Generation
One of the remarkable aspects of Capstone microturbines is their capacity for steam generation. By harnessing waste heat that’s produced during power generation, it's possible to create a highly efficient system that can simultaneously serve multiple needs. Let’s delve into the four methods by which Capstone microturbines can be utilized for steam generation:
1. HRSG Approach with Post Burner
Heat Recovery Steam Generators (HRSG) can be integrated with Capstone microturbines. In this setup, a post burner is used to increase the temperature of the exhaust gases to around 700°C. This is followed by passing these gases through a standard boiler to produce steam. The combustion is oxygen-rich, due to approximately 18% oxygen content in the flue gases after the microturbine. The oxygen level goes further down as the post burner combusts additional fuel without requiring any additional air. This approach offers flexibility in steam production and boasts an impressive efficiency that ranges from 85-95%.
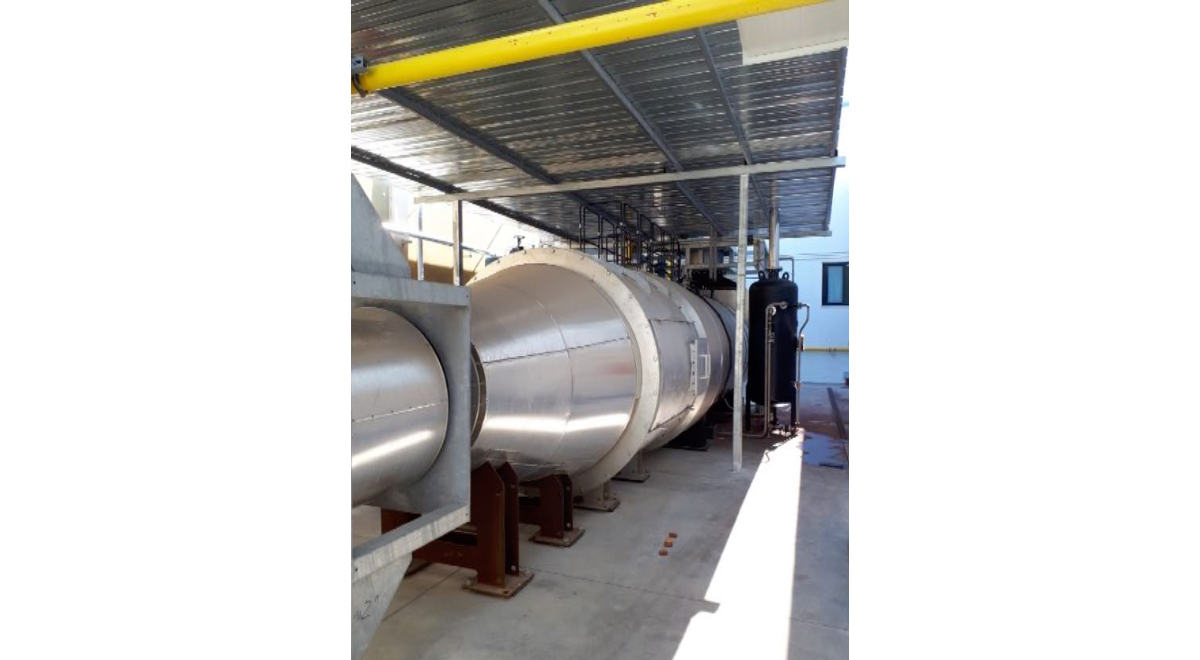
Duct burner with HRSG boiler
2. High-Efficiency Boiler Integration
A streamlined process is achieved by designing the microturbine to supply the precise amount of oxygen needed for optimal combustion within a high-efficiency boiler. If the turbine is undersized for this purpose, supplementary oxygen for combustion can be sourced externally – from fresh air. This hybrid air supply ensures that the burner can function with preheated air from the turbine, fresh air, or a combination of both. This method allows for the highest efficiency, which typically hovers around 93-95% - as per a standard steam boiler.
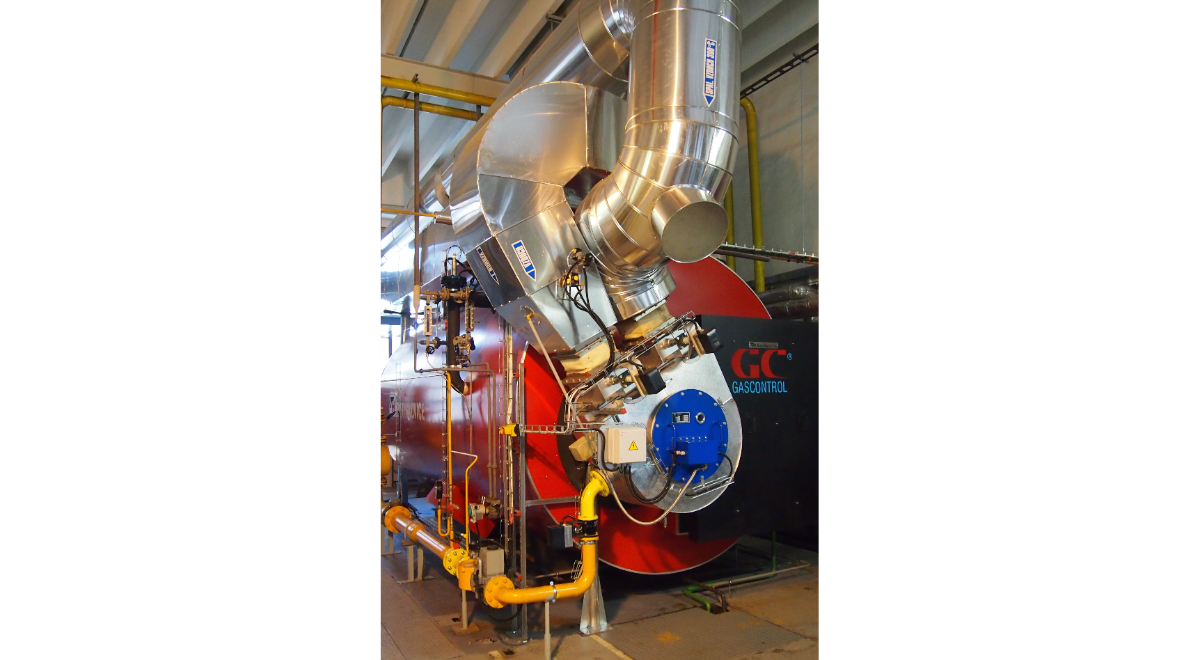
Dedicated burner for precise dosing of air and flue gas from turbine
3. Fourth Pass of Steam Boiler
In this configuration, hot flue gases are channeled through a modified standard boiler equipped with a separate fire tube pass for the microturbine’s exhaust. As the flue gases traverse the boiler, they generate steam while cooling down. The efficiency of this setup can usually be enhanced through an economizer, which further recuperates heat before the gases are expelled through the chimney.
4. Direct Steam Production
This approach involves routing flue gases through a dedicated evaporator, similar to a heat exchanger, where steam is generated according to designated parameters. The efficiency of this method is contingent on the temperature of the inlet water.
Microturbine with evaporator and economizer
Economical evaluation
Capstone microturbines offer a broad range of applications, with the capability to handle steam production from 1 ton per hour (tph) to 15 tph. This flexibility allows for an optimized energy solution tailored to specific electricity and heat requirements. By striking the right balance between electrical output and thermal energy, it's possible to maximize savings and ensure your investment in a Capstone microturbine system is highly cost-effective. In fact, the return on investment (ROI) for these systems is quite impressive, typically falling within a 3 to 5-year range. This is largely attributable to the overall efficiency of the system, which ensures that energy costs are substantially reduced over the long term. This makes Capstone microturbines an enticing option if you’re looking to upgrade your energy infrastructure with a focus on sustainability and cost-efficiency.
References
At IVITAS GREEN POWER, we understand the importance of making an informed decision, and are proud to offer you the opportunity to visit reference sites where you can witness our microturbines in action. In the Czech Republic, there are several operational installations that showcase the versatility and efficiency of our microturbines. For a more diverse view of applications, you can also visit installations from our esteemed colleagues in Italy, Austria, and Germany. It is noteworthy that Capstone’s reliability and excellence are recognized globally, with over 10,000 microturbines in reliable operation around the world. Visits to these reference sites will provide you with invaluable firsthand experience, offering an in-depth understanding of the many practical applications and benefits of integrating Capstone microturbines into your energy solutions.
For organizations and industries looking to harness this cutting-edge technology, getting to know these four methods of steam generation can be your first step in a journey towards a more sustainable and efficient energy landscape.
Stay tuned as we optimize our energy usage, explore further, and join the movement towards a greener future with Capstone microturbines.